
Silica fume can also be pelletized, whereby the silica fume is mixed with water and some cement. Compacted or densified silica fume and slurried silica fume have a bulk density that can range from 200 to 6 to 1400 kg/m 3, respectively ( ACI-Committee-234, 2006). The bulk density of the as-produced silica fume ranges from 130 to 430 kg/m 3. Some suppliers handle silica fume as a water-based slurry, and others densify and compact the silica fume, which can markedly reduce the amount of dust associated with the fine particles. To improve the ease of handling, alternative forms of silica fume have been used to overcome this practical difficulty. (Note that the surface area of silica fume is not directly comparable to that of other SCMs measured using the Blaine method.) The fine particle size of the as-produced silica fume makes it challenging to handle, from a practical perspective. The surface area of silica fume particles can range between 13,000 and 30,000 m 2/kg, measured by nitrogen absorption equipment ( Valipour et al. The specific gravity of silica fume is 2.20–2.30 ( Khan & Siddique, 2011 Tafraoui et al. In some cases, individual particles can fuse together to form small agglomerates that may range from 1 to 100 μm in size ( ACI-Committee-234, 2006). Silica fume particles are spherically shaped and very fine, having a mean size of 0.1–0.3 µm ( De Belie et al., 2017 Jiao et al., 2017 Thomas, 2013). At a temperature of approximately 2000☌ the reduction of high-purity quartz to silicon produces silicon dioxide vapor, which oxidizes and condenses at low temperatures to produce silica fume. Silica fume is a by-product from the production of elemental silicon or alloys containing silicon in electric arc furnaces. Panesar, in Developments in the Formulation and Reinforcement of Concrete (Second Edition), 2019 3.1.3 Silica fume
SILICA FUME PC
For example, the replacement of 7.5% and 15% SF by weight of cement with adequate water-reducing admixture increases the 28 days compressive strength of 100% PC concrete from 38 MPa to 65.5 MPa and 71 MPa, respectively ( PCI-Committee, 1994). Besides, the enhancement of strength by SF is due to the increasing strength in the bond between aggregate and hydrated cement product (in ITZ) ( Mindess et al., 2003). This facilitates a dense microstructure of the concrete matrix and enhances the strength of concrete. Concrete containing SF gains high early strength while GGBFS contribute to the strength gain at later ages. The combination of SF and FA increases the pozzolanic reactions, compared to that of FA substitution in the PC system alone ( Bickley et al., 1991). SF also reacts with other SCMs such as GGBFS and FA. This causes a considerable reduction of alkalis in the SF pore solution ( Diamond, 1983). In the presence of SF, the Ca–Si ratio of the C–S–H decreases, which facilitates the incorporation of other elements such as alkalis and aluminum in C–S–H. SF contribute to pozzolanic reactions of PC in the presence of portlandite and produces secondary C–S–H. Replacement of about 15% SF in cement paste allows approximately two million fine particles packed surrounding a single grain of PC ( Cohen et al., 1990).
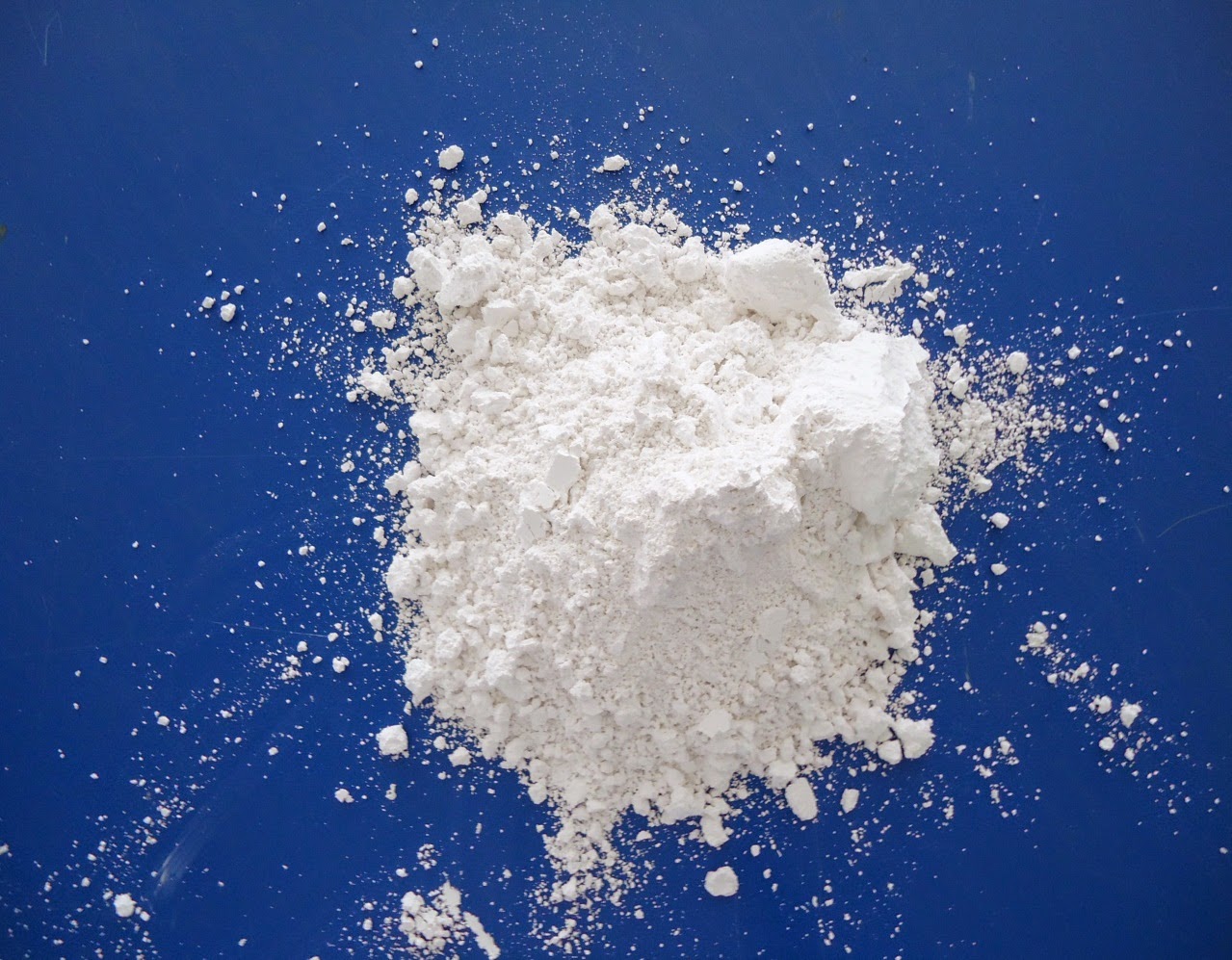
SF has physical effects as a replacement of cement in concrete. However, the blending of SF in cement may result in some loss in flexibility in the mixture corresponding to the amount of SF used ( ACI-Committee-234, 2006). The blending of SF reduces the heat of cement hydration during the initial curing period ( Lessard et al., 1983). Similarly, Icelandic cement manufacturers typically blend 6%–7% SF in cement since 1979 to mitigate alkali-silica reaction in the concrete matrix ( Idorn, 1988 Asgeirsson and Gudmundsson, 1979). Several Canadian cement manufactures are commercially blending 7%–8% SF in cement. Ternary or quaternary system (SF and other SCMs) Mortar bar drying shrinkage (28 days) increase over control (%, max)Īir entraining agent variation from control (%, max) Strength activity index at 7/28/90 days (% of control, min)
